2018-12-04
Pollutant Reduction Control and Continuous Emissions Monitoring at Waste-to-Energy Plants
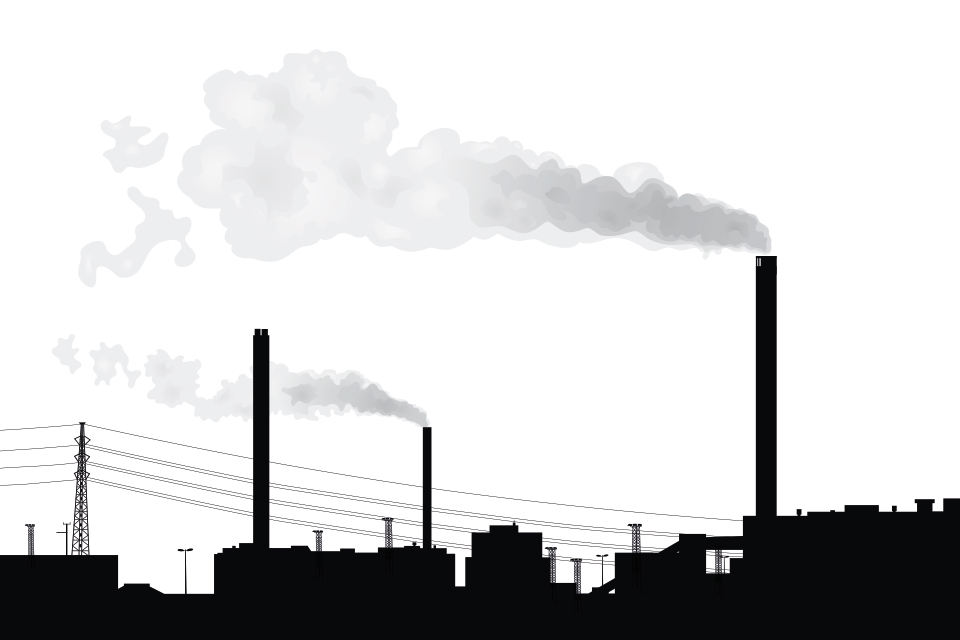
Waste is generally undesired, and best not generated at all. The second best alternative to manage waste is to recycle it. However, there is also waste that for various reasons is not recycled. Landfills have then been the old-school solution, but it is for environmental reasons becoming a less viable option. What then remains is waste incineration, in most cases while recovering the energy residing in the material. There are many different types of waste that can be incinerated, by example municipal waste, hazardous waste, and sludge. Each type of waste may call for its own type of incineration facility, varying in process and capacity depending on availability of the respective waste type.
It can be a challenge to handle all air pollutants generated in the incineration process, but it can nowadays largely be managed using various flue gas cleaning techniques. Waste incinerators therefore usually have a few things in common, irrespectively of size and waste type: the need to control the flue gas cleaning processes and the need to monitor the remaining emissions to the ambient air. This is achieved by appropriate gas monitoring techniques.
Pollutant emissions can be minimized in several ways. The most fundamental one is to generate as little air pollutants as possible at the actual incineration. This is achieved by proper control of the combustion process. With the right mix of fuel and air and at the right temperature, the formation of pollutants can be minimized. Exhaust gas recirculation can contribute to these control mechanisms.
Active flue gas cleaning methods have to be applied to address the pollutants that still are generated. A few fundamentally different types of methods can be used in waste incinerators as well as in other combustion-oriented processes: filters, scrubbers, and ammonia injection. Dust filters remove the particles, scrubbers are used above all to reduce corrosive substances, and ammonia injection with or without catalysts (SCR or SNCR) is used to reduce emissions of nitrogen oxides.
To monitor and control the scrubbing process, concentrations of SO2, HCl, and/or HF are often measured to provide signals to the injection of the scrubbing agent, typically lime or lime slurry. Proper control of the scrubber also helps protecting subsequent catalysts from the corrosive gases. NOX reduction can be achieved by injecting ammonia (NH3), then forming nitrogen and water. The objective is to minimize the NOX concentrations at the same time as no excess NH3 slips through. The reaction process required precise control of injection rates and temperatures. This is facilitated by measurements of NH3, NO and sometimes also NO2 concentrations. In either case, short measurement response times are essential to provide the required signals for the process control.
Hazardous waste from various industries may generate toxic gases other than those normally seen in municipal waste incineration plants. Compounds such as mercury, benzene, cyanide, phosgene, and other very hazardous gases may additionally have to be monitored in such cases. Hospital waste and special chemical waste may contain notable levels of iodine and bromine. HBr, Br2, and I2 may have to be measured in order to detect high levels that may need special treatment in cleaning stages, and/or to monitor emissions to the ambient air.
There are often strict regulations of emissions to air from waste incinerators, given the potentially hazardous substances that can occur in the combustion processes. The regulatory bodies can be both international, national and local. By example, the European Union has adopted the directive 2010/75/EU on industrial emissions (the IED). Emissions have to be monitored, and the results are the basis for the official emissions reports to be made and to be submitted to the authorities to demonstrate compliance with the regulations.
OPSIS’ monitoring technology is very well suited for waste-to-energy plants. It has resulted in a large number of OPSIS gas monitoring systems being deployed for continuous emissions monitoring (CEM) at waste incineration facilities throughout the world. A major reason for this is the need for the facilities to monitor a range of different types of gases as mentioned above, all which often can be conveniently measured using a single OPSIS monitoring system consisting of one or a pair of individual OPSIS gas analysers. The proven ability of OPSIS’ systems to work very well with a minimum of maintenance, despite the often hot, wet, and aggressive flue gases, is another benefit.